Posted: June 9, 2023
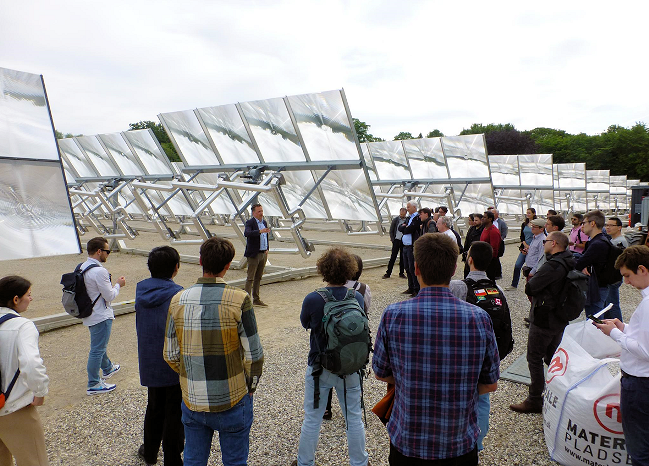
Photo: Heliac
The Danish solar district heating sector is a role model for the world. Researchers from IEA SHC Task 68 Efficient Solar District Heating met in the Danish capital Copenhagen for a project meeting and visited two innovative solar district heating examples. The first visit was to the concentrating solar heat plant in Hørsholm with its unique point-focus Fresnel collectors together with participants of Task 64 on solar process heat. The Task 68 research group also inspected the pit storage tank in Høje Tåstrup, which features a new generation of cover that reduces the heat losses significantly. In total, 36 Task 64 & 68 researchers from ten countries came together in Copenhagen to discuss the progress of their joint research and publication activities.
The study tour first took the experts to a special solar district heating plant operated by the Danish company Heliac since June 2022. The 1.6 MW solar plant consists of 2.3 m2 of Fresnel lenses that focus the direct solar irradiation on a point receiver behind them. The plant’s 144 double-axis trackers group eight lenses each. All eight receivers on each tracker are connected in series.
In Hørsholm six trackers work in series to deliver a stable output of between 100 and 110 °C in the form of pressurised water, which is fed into the district heating grid. It is the first commercial plant with the newly developed and patented lenses. Heliac has signed a long-term heat delivery contract with the utility company Norfors. “We can set target temperatures in a way which is stable and reach temperatures of up to 160 °C by adjusting the flow rate,” said Jakob Jensen, Commercial Director of Heliac. He was pleased about the many questions from the task experts: “This showed their great interest in our innovative equipment and they provided us with valuable insights into how we can explain technical parts of our solution even better,” he added.
Full control of the supply chain
Heliac was founded in 2014 as a spin-off from parent company Inmold, which works with plastic technologies. “We use a micro-structured polymer to transform a sheet of window glass into a highly efficient lens. The micro-structures are applied to the back of the window glass pane”, Jensen explained. This coating of the glass panes is done in-house at Heliac in Nivå, north of Copenhagen. “It will be a fully automated and very fast process that theoretically allows us to produce 1 GW over the year in just one production line”, added Jensen.
The receivers - the second key component of Heliac’s technology - are manufactured by a large European heat exchanger manufacturer. All other parts are standard industrial components with many potential suppliers around the world, confirmed Jensen. He sees the advantage in having full control of the supply chain without the need to purchase key components from Asia.
Innovative solar district heating
He also listed some other features that make his technology a good choice for high-temperature solutions. The two-axis tracking mode optimizes the yield per area. Jensen assumes a 20 % advantage compared to, for example, parabolic trough or linear Fresnel collectors, which are both single-axis tracked. Another plus point is the simple mounting system. Each tracker just needs one pole in the ground. This has to do with the fact that the flat glass panes do not have such high wind loads when they are placed horizontally and the structure can therefore be lighter.
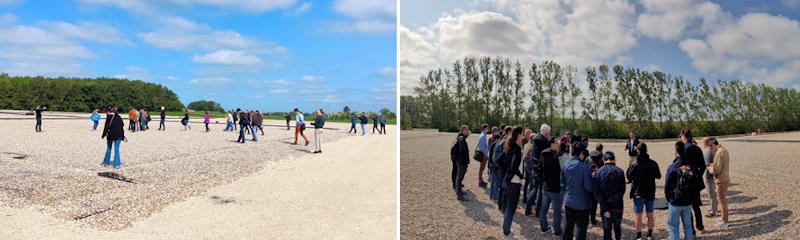
Visit to the pit heat storage tank at Høje Tåstrup. The 11,000 m2 of collector lid is walkable. The group on the right is assembled around one of the pumping wells which direct the rainwater away from the entirety of the lid.
Photos: IEA SHC Task 68
New generation of heat storage pit lids
Denmark is the pioneering company for pit heat storage tanks with more than 20 years of experience. The first larger water-filled and ground-buried basins were built in Marstal (75,000 m3) in 2011-12 and Dronninglund (62,000 m3) in 2013, among others. The main challenge of these two projects was the floating, insulated lid that was originally installed. The operators found during operation over the years that moisture accumulated within the insulation layer and caused damage beyond repair and also high heat losses. At both sites the Danish company Aalborg CSP got the job of replacing the damaged lids with a certified and patented lid design.
The lid of a seasonal storage pit has to cope with difficult operating conditions, explained Andreas Zourellis, Vice President of Technical Sales, International Markets at Aalborg CSP: “On the one hand, it has to be protected from below against water vapour that is produced by the high temperatures of 80 to 90 °C in the upper area of the storage pit. In addition, the rainwater must be drained away efficiently to minimize heat losses.”
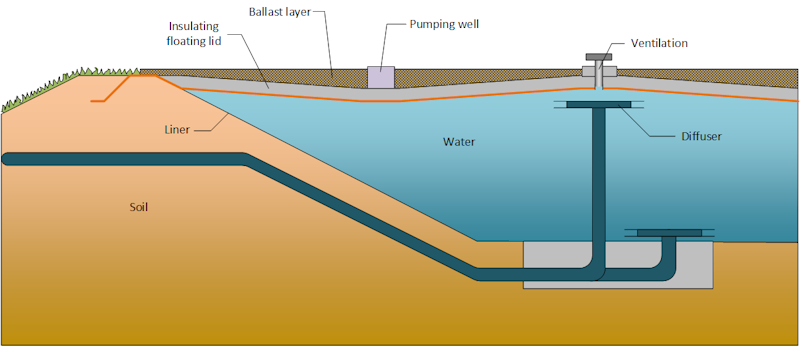
Figure 1. Scheme of a heat energy storage pit with the new lid concept developed by Aalborg CSP. It avoids moisture accumulation inside the insulation and includes automatic rainwater handling
Graphic: Aalborg CSP
Improved lid technology has reduced heat losses significantly
This proven lid technology developed by Aalborg CSP divides the cover into evenly sized squares with a slope towards the centre of each square, in which a pumping well directs the rainwater away from the entirety of the lid. Between the squares, air-vents are built-in that help avoid air build-up inside the pit. “In Dronninglund the replacement of the lid reduced the losses from the storage pit down to 8 % over the year,” said Zourellis, summarising the monitoring results after more than one year of operation. In addition, the new lid design reduces maintenance of the seasonal storage pit.
This lid technology was also used in the newly built storage pit at Høje Tåstrup near Copenhagen that the Task 68 experts visited. The 70,000 m3 heat storage pit has a capacity of around 3,300 MWh and is intended to reduce expensive peak loads in the district heating network Høje Tåstrup Fjernvarme. This makes the storage pit at Høje Tåstrup “one-of-a-kind” since it is the first operational storage pit with multiple charging/discharging cycles within a year (e.g. 26 cycles) as opposed to the traditional seasonal storage pits coupled with solar thermal energy (approx. 1 cycle). It is charged with heat from the Greater Copenhagen transmission grid owned by VEKS, which shares the ownership of the heat storage pit with the district heating company of Høje Tåstrup.
Websites of organisations mentioned in this news article: